Why Should Viscosity be Calculated Accurately for Positive Displacement Pumps?
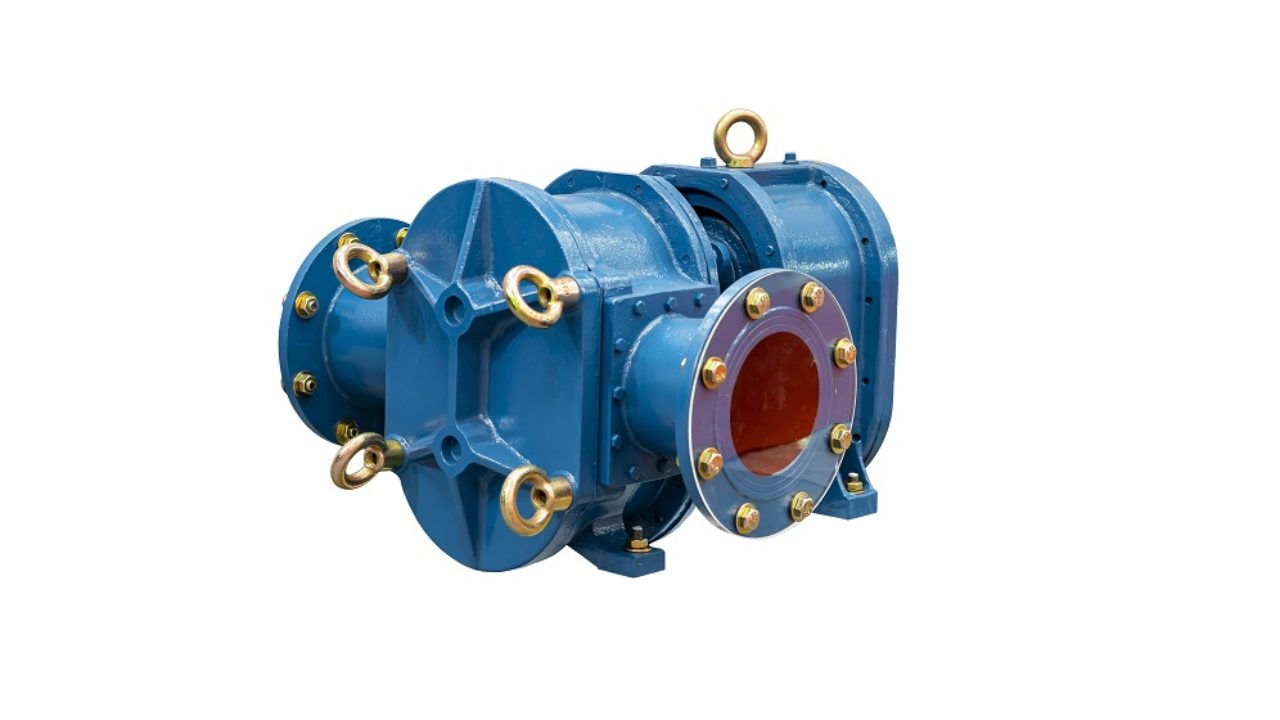
Pumps are used in various applications across multiple industries. They are vital in liquid handling and liquid management. One of the biggest concerns with pumping systems is what happens when the environment changes and the pressure changes in the system due to lack of supply. Positive displacement pumps are not impacted by system changes. That is why they are widely used in settings where the pressure changes frequently throughout the course of any given day.
Viscosity Calculation is Vital
During the design phase of positive displacement pumps it is necessary to analyze the type of liquid to be handled. It is important for the specific factors of the liquid to become known. Even if the makeup of the liquid is:
- Variable
- Unknown
- Proprietary
Those factors still need to be determined to properly design the pump to handle the given conditions and type of liquid.
What is a Positive Displacement Pump?
One of the biggest advantages of positive displacement pumps is their ability to generate even flow rates. They are able to do this by operating in a repeating cycle. This is achieved by using one of the following three systems:
- Reciprocating System
- Diaphragm System
- Rotary System
At the most basic level, a positive displacement pump efficiency rating is higher than other types of pumps. This is due to the fact that they draw liquid into a chamber from an inlet valve and then it is expelled through the outlet valve. When the proper pressure has been met, then the system discharges the liquid from the chamber.
Types of Positive Displacement Pumps
Adaptable to almost any project, the pumps come in a variety of types.
- Screw Pumps
- Plunger/Piston Pumps
- Vane Pumps
- Air Operated Double Diaphragm Pumps
- Rotary Gear Pumps
Inaccurate Data Can Result in Unforeseen Consequences
There are some situations in which data is incomplete during the manufacturing process. This is not a best business practices as having inaccurate data can result in major impacts to the system, the pump, or both.
Lower Than Expected Viscosity Issues
For instance, a positive displacement pump is designed for a specific fluid viscosity. If the viscosity is actually lower than predicted, the pump will produce less flow than expected. This lower flow may cause reduced production, translating to lower output and lower revenue.
For maintenance, operating the pump in a lower flow than predicted can lead to bearing wear and expensive repairs.
Higher Than Expected Viscosity Issues
When a pump is designed to for a specific viscosity level and the fluid has a higher viscosity than expected, in the operational environment, it can have a negative impact as well. This would mean a higher-than-expected flow, which would cause the pump to operate at a higher rate than normal. This would draw more power, which in turn, could trip the motor’s protection circuit.
In extreme cases, the pump might not function correctly due to improper suction at the pumping elements.
Testing and Data Correction
Once the manufacturer has the needed data and detailed information, they can design the pump. As the design process begins, there might be additional questions to garner more information about the operational nature of the pump. There are no two pumps that are identical. This is due to the fact that there are slight differences in the manufacturing process and in the operation environment.
Some of those factors in the operational environment can include:
- Variations in System Fluids
- Variations in Fluid Pressure
- Variations in Driver Speeds
It becomes difficult, if not impossible, to test for every possible operational condition. This is why it becomes so important to gather as much information as possible to make informed decisions during the design phase. It is also important to rely on standardized testing and performance ratings. By doing this, the manufacturer can say with confidence, what the pump’s likely performance will be before it is ever shipped to the customer’s site.
Testing Phase and Viscosity Determination
The testing process and data gathering step includes the following:
- Sample Selection
- Fluid Calibration
- Temperature Measured
- Viscosity is Determined
It is important the fluid sample collected be representative of the fluid that will be in the operational environment. If it is not, the findings will be inaccurate. Once the fluid is collected, it is calibrated by recording the temperature. Once this is done, the viscosity of the liquid can be determined and the pump correctly calibrated to function with optimal efficiency in that specific operation environment.
During the testing phase, adjustments can be made based on the following:
- Customer’s Operations Environment
- Customer’s Fluid Viscosity
- Customer’s Operating Speeds
- Customer’s Operating Pressures
This then allows the manufacturer the ability to estimate the input power necessary to have the pump operate at an optimal level. That is why it is absolutely necessary to receive accurate and complete information to ensure the proper calibration of the selected displacement pump.
Final Thoughts
Industrial pump systems are more than just a series of pipes, joints, and pumps. They are the lifeblood of a liquid handling businesses. With properly calibrated positive displacement pumps, the system can work at an optimal rate which improves efficiency and longevity of the pumps and the pumping system. When pumping systems are properly calibrated there are less breakdowns and less time offline. All of which spells an improved bottom line.
Let Vissers Sales Corp. help select the proper pumps for your application. Reach out to us today.